DISC (Industrial Management & Supply Chain) brings together numerous forms of expertise covering industrialization, production, product management and logistics in order to meet customer requirements in all countries
The worldwide market for laboratory analysis is extremely varied in terms of medical practice, organization, legislation, regulatory requirements and financing. Therefore, Stago must be the "solution provider" in all of these sets of circumstances.
DISC also has staff specializing in "ongoing improvement" (validation of methods, metrology, change management), supply, purchasing, engineering and maintenance.
Ensuring customer satisfaction is our ultimate goal.
Broad-Ranging Activities and Expertise
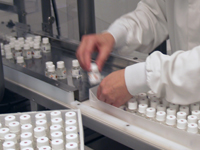
Even the most incredible innovation would have no meaning and no future without the ability to transform it into a standardized industrial product.
In terms of laboratory analysis, reliability and reproducibility of the analytical results delivered by a laboratory constitute key factors in the health care subsequently provided to patients.
For this reason, the systems (analytical devices, reagents, consumables, services) that we sell must be beyond reproach.
3 Key Areas of Expertise
- Instrumentation: wide-ranging expertise in robotics, data processing, electronics, electro-mechanics, optical measurement, methodology, micro-fluidics, for example
- Reagents: control over method process standardization, high volume production, control of starting materials and biochemistry techniques (e.g. enzymology, immunology, purification) and chemisty
- Disposables: primarily single use measuring cuvettes (development, industrialisation, etc.)
From Industrialization to the Final Customer, Worldwide
Manufacturing Expertise
Production activities follow a continual improvement process in order to allow us to:
- Ensure processes remain as flexible as possible so as to be constantly supply our customers
- Optimize delivery times
- Continually offer customers robust products of the highest possible quality
In order to meet the expectations of our customers, both direct (laboratories) and indirect (distributors, subsidiaries), we focus on:
- Safety in our production facilities
- Optimization of ergonomics (assembly, integration) in order to ensure better productivity (in both qualitative and quantitative terms)
- Reduction of cycle times (i.e. the time required to manufacture a product; the shorter this time, the less risk of stock shortages)
- Integration of quality control in all stages of manufacturing processes
Expertise in Purchasing of Starting Materials
- The ability, starting from the "upstream" stages of product design, to select the best supplier consistent with the requirements of both designers and producers
- Following selection, suppliers are monitored and evaluated throughout the entire life cycle of products.
- Stago has more than 250 active suppliers for 3000 items used as starting materials and ingredients.
Ongoing improvement in this area is essential to:
- Secure supply of starting materials and ingredients
- Optimize stock levels
Expertise in Distribution
Since Stago exports 85% of its production, complete control of logistics is absolutely vital and consists of expertise in freight management (air, maritime, cold chain, packaging, customs regulations etc.) and in stock and process flow management.
For its worldwide distribution, Stago currently uses two logistics platforms and satellite warehouses in accordance with geographical requirements. In addition to the delivery of products directly to end users and distributors, these centers also provide support to technical departments with respect to rapid delivery of tools and spare parts.
Continuous improvement processes are in place to reduce order processing and preparation times.
Throughout the entire company, but particularly in the Research & Development as well as the Industrial and Supply Chain Departments, a carefully structured management method, developed along the lines of "Lean Six Sigma" is used to provide a more global view of processes to ensure continual quality improvement.